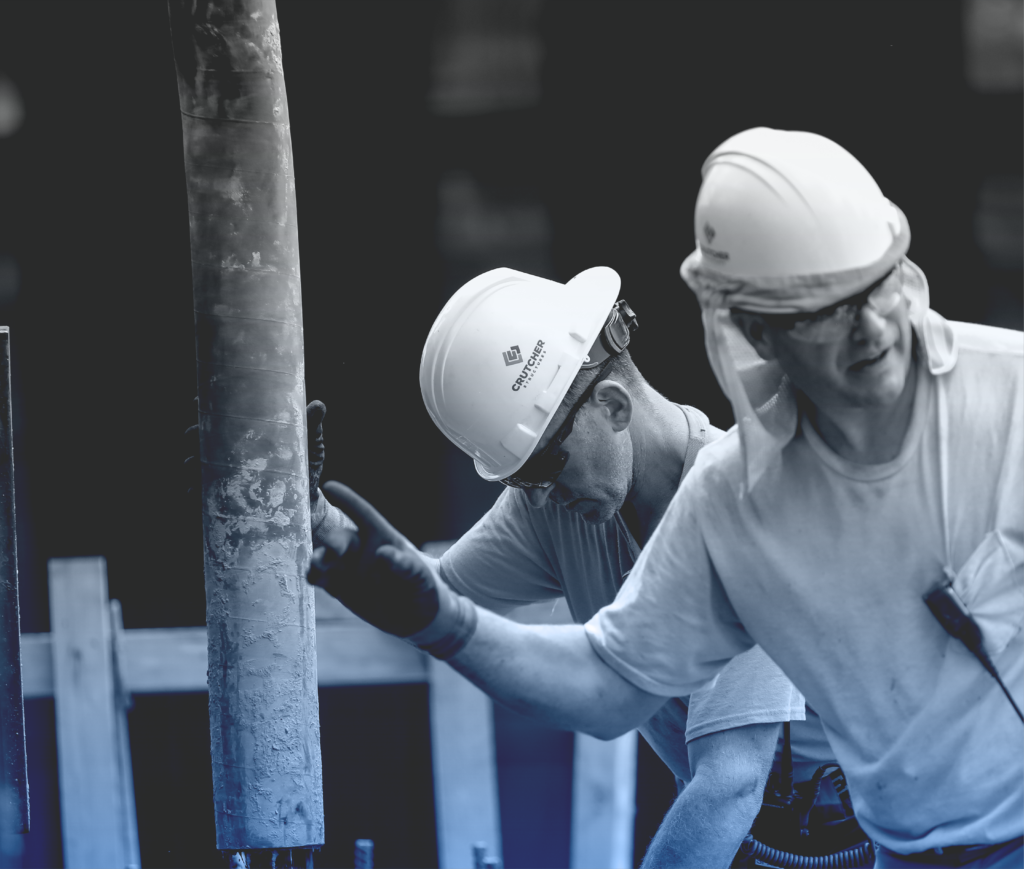
What We Do
FORGED FROM A CENTURY OF BUILDING.
Crutcher Structures is a subsidiary of Lease Crutcher Lewis—a Pacific Northwest General Contractor operating in Washington and Oregon. Leveraging over 139 years of history and rich tradition as a builder, Crutcher Structures capitalizes on the benefits of standardization and specialization to deliver unsurpassed value for our customers.
Our core business is the delivery of structural building frames, including concrete, steel, timber or composite. Our relentless planning, proven systems, strong communication and superior craftsmanship are best in class.
Crutcher Structures can also provide a wide breadth of supplementary construction services to meet the unique needs of our customers. Whether you need comprehensive project planning, scheduling, site logistics, building information modeling, etc., we are prepared to customize a scope of services to meet your exact project needs. This client-centered, tailored approach provides an offering unparalleled in the specialty subcontractor marketplace.
Give us a call and let’s discuss a partnership that will help you achieve your goals.
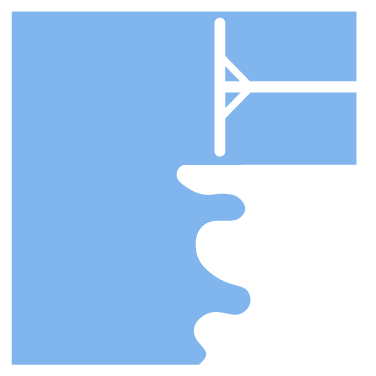
CONCRETE CONSTRUCTION
Concrete forming | Concrete placement | Concrete finishing | Precast concrete installation
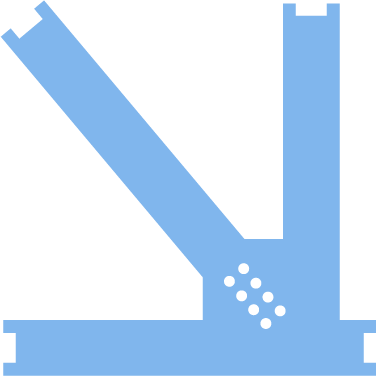
STEEL CONSTRUCTION
Steel erection | Steel stair installation | Architectural metals | Railings | Canopies
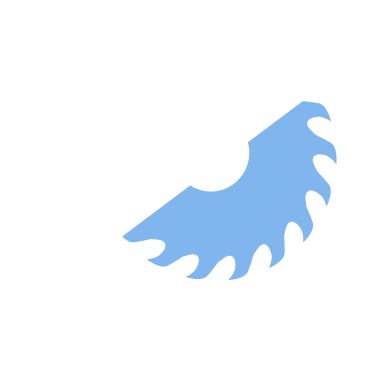
SUPPLEMENTARY CONSTRUCTION SERVICES
Mass timber | Doors, frames and hardware | Millwork | Miscellaneous specialties installation
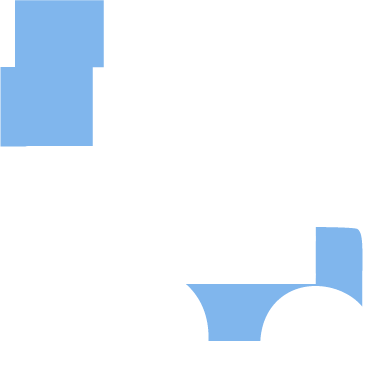
CONSTRUCTION SUPPORT SERVICES
Tower cranes and manlifts | Survey and 3D scanning | Equipment rental
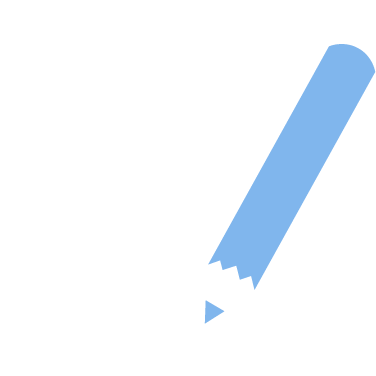
PRECONSTRUCTION PLANNING
Design-build and design-assist | Scheduling | Constructability evaluation | Sustainability consulting | Site logistics and planning | VDC modeling
Our Experience
Crutcher Structures has helped deliver some of the region’s most challenging projects. Our teams utilize our rich history as a general contractor to build projects holistically, identifying and mitigating challenges before construction even begins.
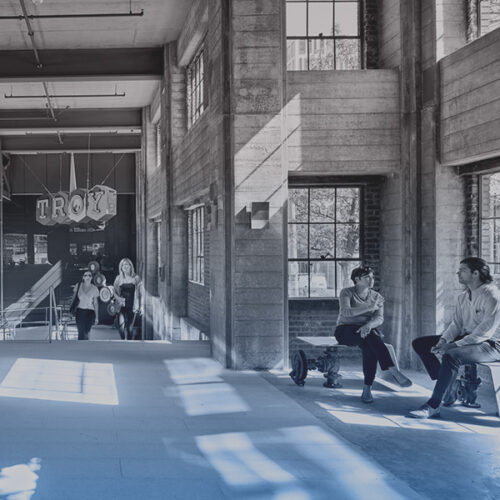
TROY BLOCK

TERMINAL 106
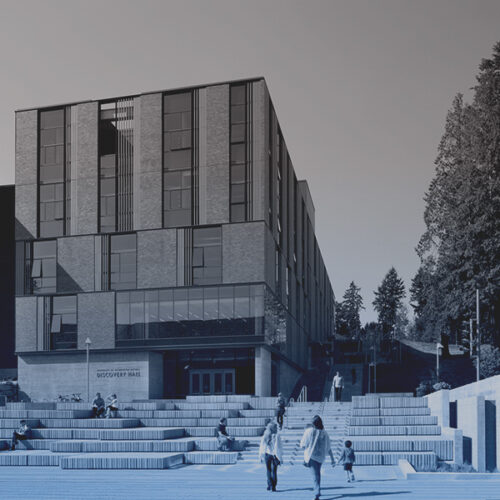
DISCOVERY HALL
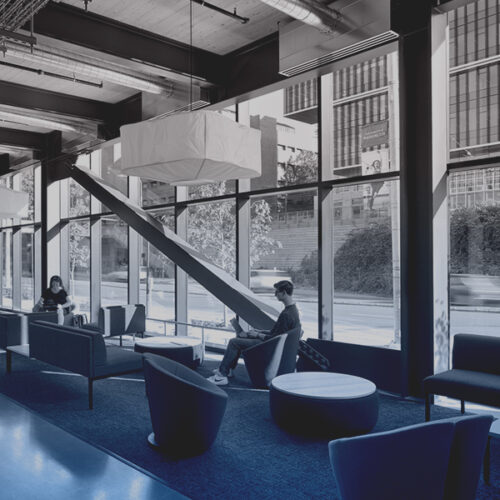
HEALTH SCIENCES EDUCATION BUILDING
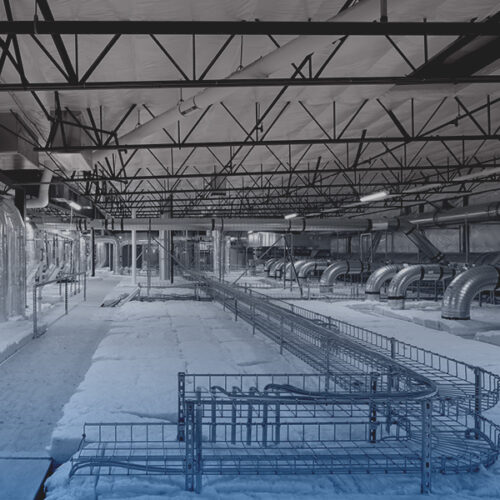
BUILDING 6
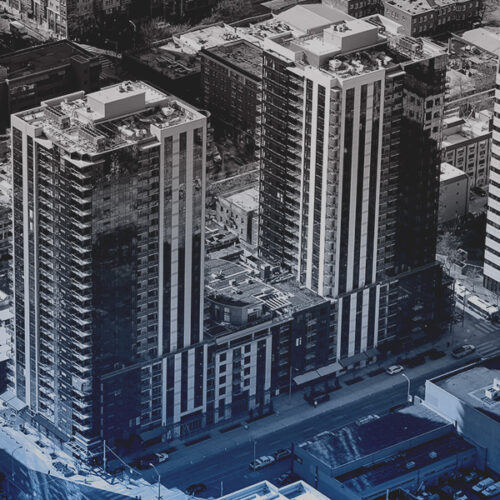
VIA6
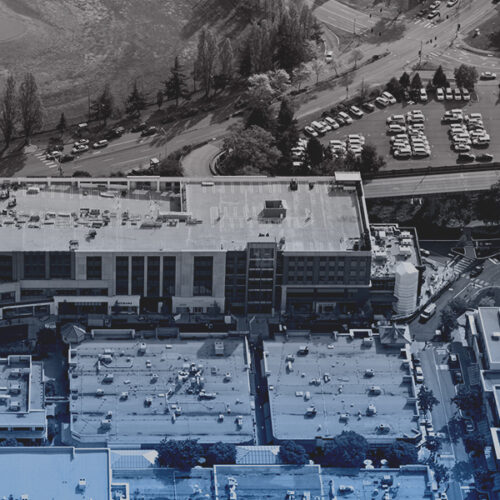
VILLAGE SOUTH PARKING GARAGE
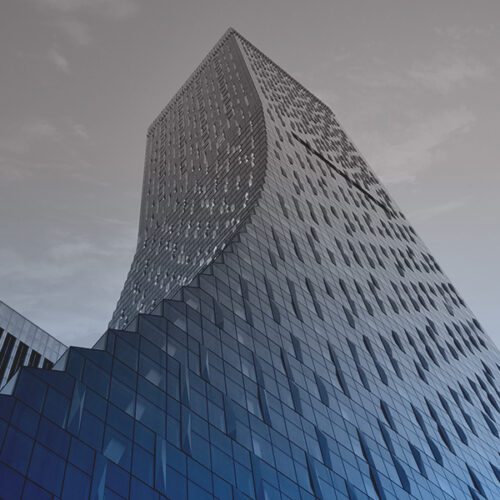
RAINIER SQUARE
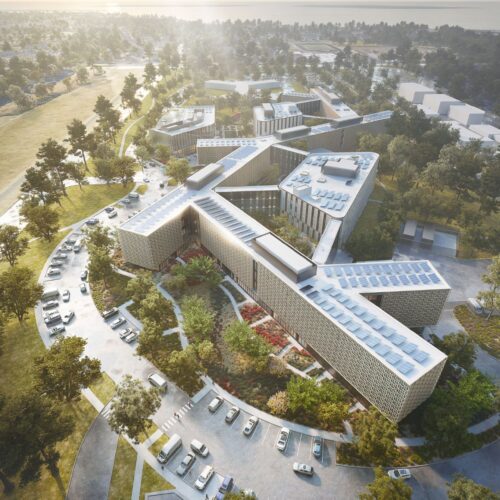